Now that you have a better understanding of when to use abrasive blast finishing, let’s look at another effective parts cleaning process that KVF Quad specializes in. (If you missed the post about abrasive blast finishing, check it out here.)
Why Use Shot Blasting
Shot blasting is an aggressive process that generates anchor surface, remove tight mill scale, previous coatings, or foundry slag. This leaves components with a uniform exterior surface finish that is visually appealing and more consistent when used in a manufacturing application.
Again, a variety of media types are available with KVF Quad’s shot blasting equipment and are selected based on customer specifications and required surface finishes. At KVF Quad, we can manage most sizes, shapes, and types of parts for this cleaning process.
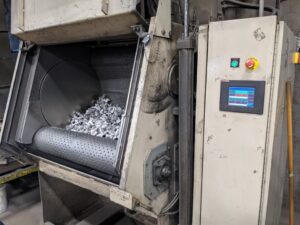
ALMCO Shot Blast Equipment
You can see our ALMCO shot blast equipment in the image above. The shot blasting processes are controlled by a PLC inside the cabinet, which is run by the exterior touch screen visible in the picture. The rubber belt is vulcanized, preventing premature wear and protects parts while moving on the belt and after the blast process is finished. Media is reused via an auger in the back of the machine.
When is Shot Blasting the Best Option
Shot blasting is the ideal cleaning process when parts or materials are dense or are small enough to process in the shot blast machine. This not only improves surface finish but is a cheaper option as well. Shot blasting also provides some stress relief to parts as they are processed when the media used impacts the surface of the part and releases stress caused by the welding, forming, or casing.
To answer all your questions or learn more about shot blasting at KVF Quad, reach out to our experts by emailing sales@kvfquad.com or calling 309-755-1101.